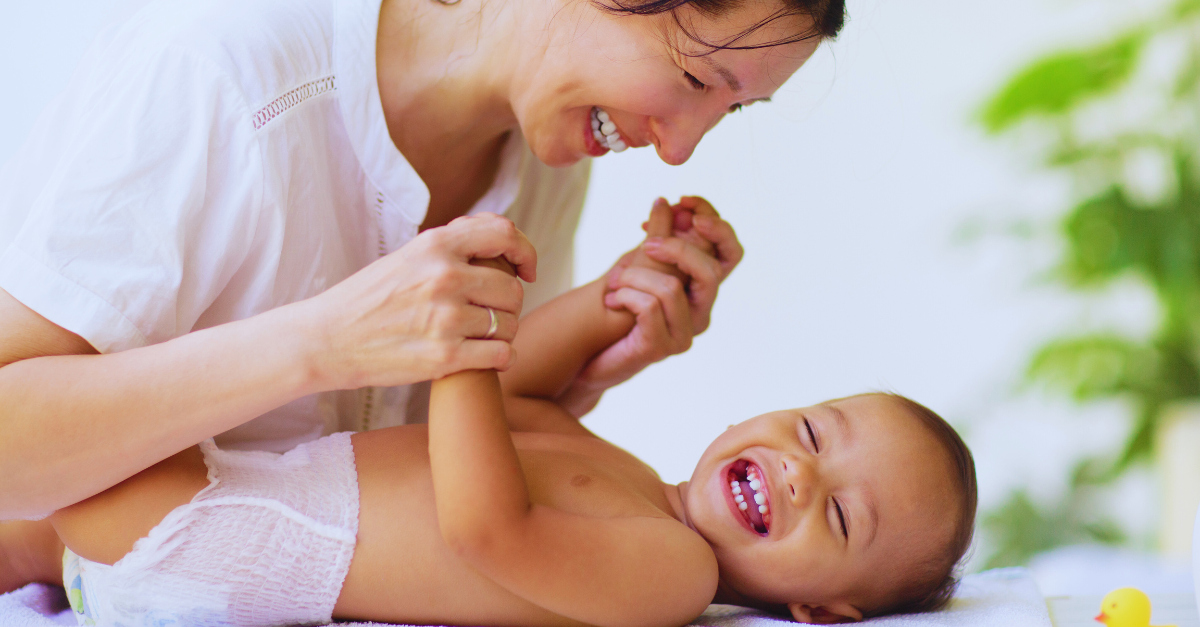
Are Your Baby Diapers Safe? The Tech Behind Quality Hygiene Products
Every parent wants the best for their baby — comfort, safety, and protection.
But what happens when a diaper doesn’t absorb properly or a sanitary pad fails to provide the comfort needed?
One of the main challenges in hygiene manufacturing is ensuring the constant quality of hygiene products, such as diapers, adult incontinence and sanitary pads.
However, poorly manufactured hygiene products can lead to discomfort, leaks, and even skin irritation, affecting the well-being of the little ones.
Yet, traditional quality control methods rely on destructive testing, which means only a small fraction of products are checked, leaving room for defective products to slip through.
If a defect is found, an entire batch may need to be rejected, leading to significant waste and financial loss.
At TiHive, we built a system that offers a new way to approach quality control. Using Terahertz technology, our system inspects every single product in real time, directly on the production line.
It identifies defects, measures material thickness, and monitors the even distribution of key components, like super absorbent polymers (SAP), without damaging the products.
By switching to this real-time, non-destructive terahertz (THz) inspection system, manufacturers can guarantee higher product quality while reducing waste and production costs.
Typical machine issues that are related to quality can take days or even weeks to debug, therefore impacting the productivity of the production lines. On the other hand, raw material variability, notably SAP, leads to both quality variability and increase of the cost of goods sold (COGS).
Our solution helps our customers increase their production uptime, whilst reducing wasted raw materials and maintaining quality. We estimate a return on investment of up to a million euros per year on a typical absorbent hygiene production line.
In this article, we cover how our solution improves hygiene product quality through better Quality control.
The Challenges of Traditional Quality Control
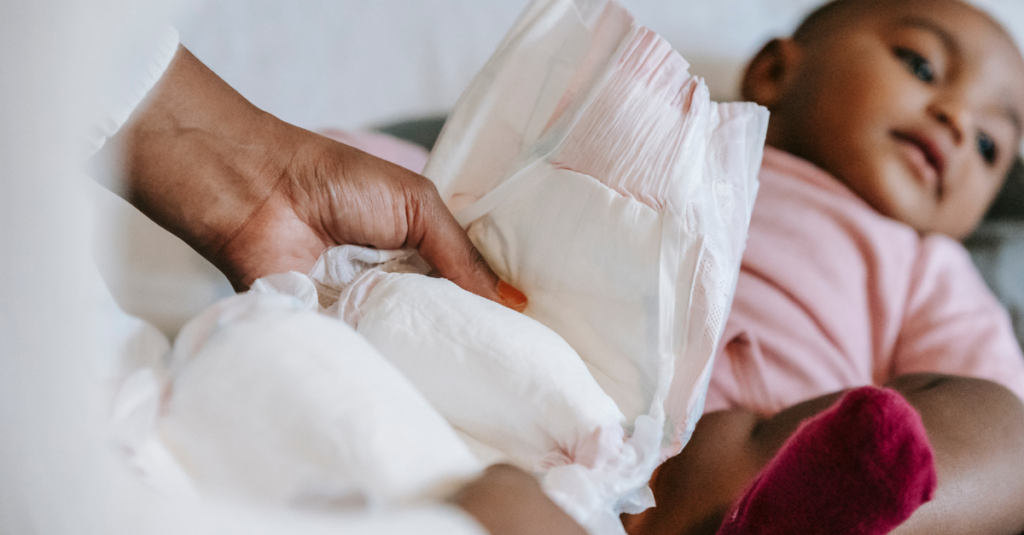
For years, hygiene product manufacturers have relied on sampling-based quality control. A few products are selected from each batch, taken to a laboratory, and tested for absorption capacity, material integrity, and overall performance.
However, this method has several limitations:
- It is slow and inefficient. Testing in a lab takes time, delaying decision-making.
- It leads to unnecessary waste since these tests are destructive
- It is not representative. A defect in a single batch might go unnoticed if the tested samples have no issues.
And lastly, it causes financial losses. If a defect is detected too late, entire batches must be discarded, resulting in wasted raw materials and increased costs.
With increasing pressure to improve sustainability and reduce costs, manufacturers need a more reliable and efficient way to inspect 100% of their products without slowing down production.
How T-MONIT Transforms Quality Control and Quality Assurance
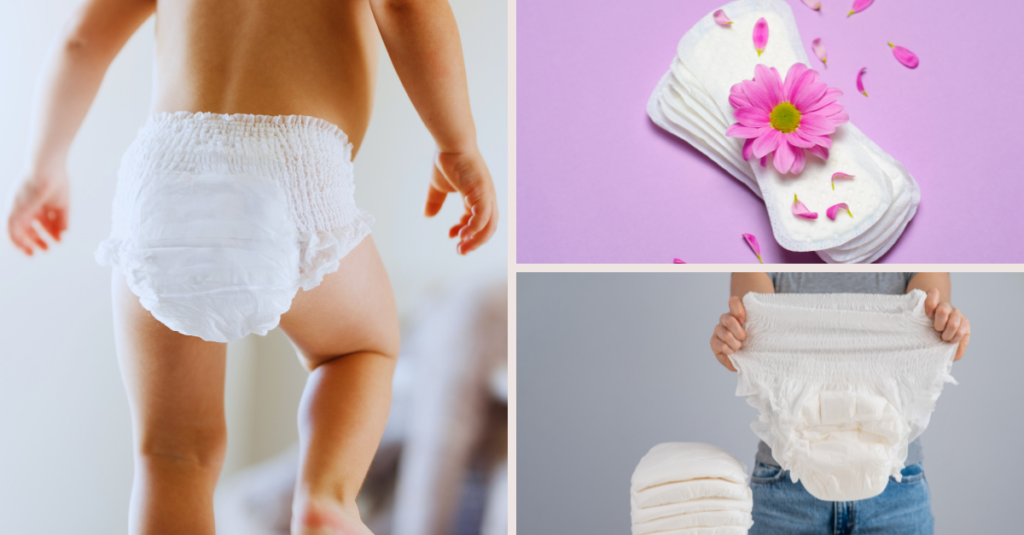
T-MONIT is a real-time, non-destructive inspection system designed to help manufacturers leverage terahertz & AI to monitor the quality of all products.
By using terahertz waves, it can see through materials without damaging them, making it possible to detect defects and measure product properties directly on the production line.
In the hygiene product industry, it allows a specific use case that is measuring the precise amount, distribution and grammage of super absorbent polymers. Through our advanced algorithms, T-MONIT detects various types of defects such as asymmetry, layer folding, hard spots, underdosage and overdosage, missing layers, 3D cores and channels, zonal analysis and other.
Key Benefits:
Detecting Defects Before They Become Problems
One of the biggest advantages of T-MONIT is its ability to identify issues before they lead to costly recalls.
Instead of waiting until the end of the production process, manufacturers can now detect problems as they occur.
Whether it’s an uneven distribution of SAP, missing layers, or inconsistencies in thickness, T-MONIT provides instant feedback, allowing QA, QC & production teams to adjust settings in real time and prevent defective products from reaching the market. It enables real-time root-cause analysis, leading to higher productivity rates, whilst maintaining the quality standards.
Optimizing Material Usage and Reducing Waste
Inconsistent material distribution and dosage not only affects product quality but also leads to unnecessary costs. T-MONIT helps manufacturers use raw materials more efficiently by ensuring that SAP, fibers, and other components are applied evenly across each product and at the correct amount.
This means:
- No overuse of expensive materials
- No need for excessive safety margins
- Fewer rejected batches
Ensuring Compliance and Consumer Satisfaction
A single defective batch can damage a brand’s reputation and lead to expensive recalls. We help manufacturers ensure that every single product leaving the production line meets the highest quality standards.
This not only helps with regulatory compliance but also enhances consumer trust and satisfaction.
This technology not only aids in defect identification but also in understanding the root causes of these defects, promoting seamless integration with automated repair systems. The result is a substantial improvement in safety and quality control within automotive manufacturing processes.
A Smart Investment for your lines
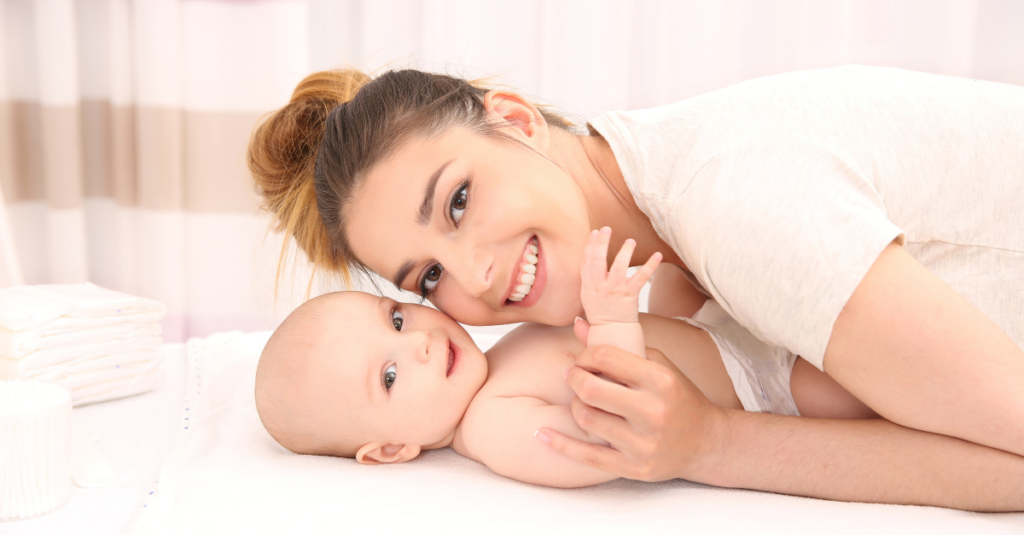
Switching to real-time, non-destructive inspection makes manufacturing smarter, more efficient, and more sustainable. T-MONIT gives manufacturers the ability to see inside their products in real time & at very high speeds, catch defects early, and optimize material usage, leading to significant cost savings and a lower environmental footprint.
For companies looking to reduce waste, cut costs, and ensure consistent product quality, integrating our non-destructive system might just be a game changer!
Interested in knowing how we’re also reducing raw material waste for cost-effectiveness with this solution? Stay tuned for our next article!
💡 Want to learn more? Contact us today and request a free demo to experience firsthand how our solution can benefit your production line.